
Check the Interconnection of the Two C-sections (Section D1.1): Thus, this limit state is an important design check for continuous span beams. Combined Bending and Web Crippling (Section C3.5):įor continuous span members, the combination of high compression stresses resulting from concentrated loads and bending stresses may occur at intermediate supports.

The coefficients and safety factor tabulated in Table C3.4.1-1 are not appropriate because these coefficients, although indicated to be valid for “built-up sections,” were experimentally developed for only I-shaped sections. The appropriate coefficients and safety factor are provided in Table C3.4.1-2. Web crippling must be considered if the box beam is supported on its bottom flange, and no web stiffener or clip is provided at the support location. If the box beam is uniformly loaded, web crippling need only be considered at the end support. Combined Bending and Shear (Section C3.3):įor continuous span members, the combination of high shear and bending stresses may occur at intermediate supports. Because of the thin web material, buckling is the controlling shear limit state. However, the available shear capacity per web may be computed based on the limit states of shear yielding, shear inelastic buckling or shear elastic buckling. If the span length is less than L u, no intermediate braces are required to achieve the yield moment as computed by Section C3.1.1 of the AISI specification, M axo = S xe F y / Ω Check Shear Alone (Section C3.2):įor cold-formed steel members, shear alone is typically not a controlling limit state. This design check is achieved by evaluation of the following equation: Because for a closed box member in bending, lateral buckling is unlikely, the AISI Specification first requires the evaluation of the critical unbraced length for which overall buckling is not a limit state. The two interconnected C-sections are assumed to behave as a closed box member. The following example illustrates the design steps for a built-up box beam. Figure C-D1.1-1 (AISI S100-07C).Īdditional limit states that must be considered in the design of a flexural member are further defined in the AISI S100 provisions and include Bending, Shear, Combined Bending and Shear, Web Crippling, and Combined Bending and Web Crippling. D1.1-1, define the fastener spacing along the length of the member (Figure 1).įigure 2. Q = Design load on beam for determining the longitudinal spacing of connections. M = Distance from shear center of one C-section to mid-plane of web T s = Available strength of connection in tension (Chapter E) G = Vertical distance between two rows of connections nearest to top and bottom flanges S max = L/6 or, whichever is smaller (Eq. The maximum longitudinal spacing of connections (one or more welds or other connectors), s max, joining two C-sections to form an I-section shall be:

The AISI S100 provisions for Flexural Members Composed of Two Back-to-Back C-Sections (D1.1) are as follows:
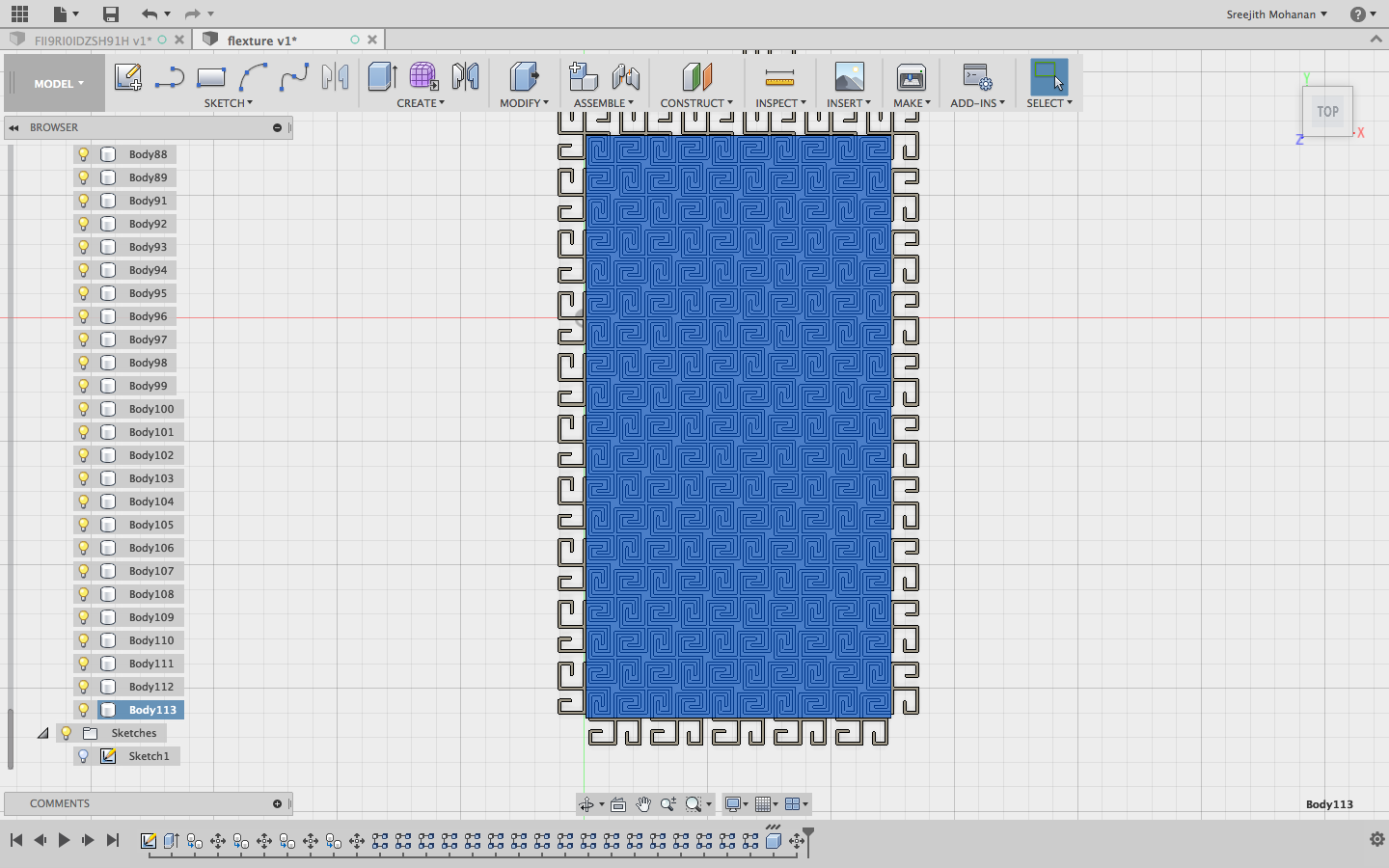
The same shear flow exists in a box-shaped section therefore, the S100 provisions could apply to form a box-shaped section with the two C-sections oriented lip-to-lip. The AISI S100 provisions are based on stabilizing the shear flow in the flanges. This article illustrates the extrapolation of S100 Section D1.1 provisions to a box beam configuration. For built-up members to act as a single composite unit, the members must be connected with sufficient fasteners at the maximum spacing as calculated below. Section D1.1, but does not contain design guidance for a box-section formed by orienting two C-sections lip-to-lip. The American Iron and Steel Institute’s AISI S100 contains design provisions for built-up flexural members consisting of two C-sections oriented back-to-back to form an I-shaped section, i.e. A box beam configuration may be used at openings in a floor or wall framing assembly.
